近年、組織業務の効率化において「見える化」という施策が注目を集めています。
見える化にはさまざまなメリットがあり、見える化に取り組むことで今まで見落としていた新しいソリューションが模索できます。
しかし、製造業における見える化とは一体何なのか、詳しい説明ができないという方も多いのではないでしょうか。
当記事では、製造業における見える化について解説します。
あわせて企業の見える化事例もいくつか紹介するため、製造業の見える化について理解を深めたいという方は、ぜひご一読ください。
タスク・プロジェクト管理を
シンプルにわかりやすく
Jootoはカンバン方式のタスク・プロジェクト管理ツールです。
直感的に使えるレイアウト、親しみやすいシンプルなデザインが特徴です。
まずは無料で体験してみる
目次
製造業における「見える化」とは
見える化とは可視化とも呼ばれ、言葉の通り「目で見る管理」という古くから活用されてきた言葉から派生した言葉です。
見える化は製造業はもちろんさまざまなビジネスの現場で使われています。
製造業における見える化とは、生産情報をデータ化し、数値を客観的に捉えることで業務の効率化を図る施策を指します。
属人化していた業務を明らかにすることで、企業として取り組む課題を見つけやすくなるでしょう。
製造業での「見える化」の目的とメリット
製造業での見える化施策には、さまざまな目的とメリットがあります。
見える化施策を検討している方は、目的とメリットを十分に理解した上で実施しましょう。
製造業での見える化の目的とメリットは以下の通りです。
- 作業進捗を把握し効率的な作業を行う
- 自社が抱える問題を発見し解決に導く
- 社内全体で業務プロセスを把握し品質面の安定性を保つ
ここでは、3点について詳しく解説します。
作業進捗を把握し効率的な作業を行う
見える化には作業進捗の把握や効率的に作業をするという目的があります。
製造業の見える化を進めたいと考えている場合、IoTの導入を検討しましょう。
IoT(Internet of Things)とは、直訳すると「モノのインターネット」という意味になり、機械がインターネットを経由しさまざまなデータ通信をすることを指します。
IoTを導入すると、機械の稼働状況はもちろん作業進捗や在庫量などをリアルタイムで把握できます。
つまり、IoTの導入で鮮度のあるデータを好きなタイミングで収集できるようになります。
現場の状況をリアルタイムで把握できれば、進捗に応じて製造ラインの人員配置を変更することが可能になり、効率的に作業を進められるでしょう。
自社が抱える問題を発見し解決に導く
見える化施策を推進すると、自社が抱える問題を発見し、解決に導くことができます。
機械から送信されるデータを元に分析し俯瞰的な目線で物事を捉えられるのもメリットの1つです。
現場の状況をデータ化し、進捗を確認することで「ムダ」や「ムラ」に気付きやすくなるでしょう。
また、現場の状況を確認したいと考えた場合、これまでは直接工場に向かっていました。
しかし工場にある機械にカメラを設置し、稼働状況を遠隔からモニタリングできるようにすることで直接工場へ向かう回数を減らせます。
巡回に割いていた時間を他の業務に充てられるため、移動時間などにかかっていた「ムダ」が解消されるでしょう。
また、リアルタイムで工場の様子が確認できるため、故障などの早期発見はもちろん、早い段階で対策を打てる点もメリットの1つです。
社内全体で業務プロセスを共有し品質面の安定性を保つ
製造業における見える化推進の目的として、社内全体で業務プロセスを共有する点が挙げられます。
業務プロセスを共有し標準化することで、完成品のムラをなくし品質面の安定性が保てるでしょう。
また、見える化は人材育成の面でも重要な役割を果たしています。
熟練者のスキルをマニュアルに落とし込むことで、個人だけでなく若手社員のスキルアップにつながります。
タスク・プロジェクト管理を
シンプルにわかりやすく
Jootoはカンバン方式のタスク・プロジェクト管理ツールです。
直感的に使えるレイアウト、親しみやすいシンプルなデザインが特徴です。
まずは無料で体験してみる
製造業の見える化事例

見える化を採用して成功した企業は多くあります。
企業の特性に応じて自社で使いやすいシステムを構築することで、業務の効率化が期待できます。
以下は製造業で見える化施策を実行し、成功した事例です。
- 見える化事例1:トヨタ自動車の「かんばん方式」
- 見える化事例2:富士通の「COLMINA」
ここでは、2つの事例について詳しく紹介します。
見える化事例:トヨタかんばん方式
トヨタ自動車では、「かんばん方式」と呼ばれるタスク管理・進捗管理を目的として開発した見える化のツールを採用しています。
かんばん方式は「いつ・どこで・何を・どれだけ使用するか」を明記し、指示書どおりに生産することで「ムダ」をなくすという仕組みです。
指示書を見るだけで現在どのような工程をしているのかが明確に分かり、後工程もスムーズに進められるため、効率的に作業が行えます。
トヨタ自動車は、かんばん方式を用いた結果、「ムダ」をなくし「必要なものを、必要な時に、必要なだけ」製造することを実現しています。
工程間の流れを効率的に制御する方法であると同時に、当時多くの在庫を抱えていたトヨタ自動車の画期的な在庫管理方法であったと言えるでしょう。
かんばん方式は、人工知能(AI)などのデジタル技術を活用したスマートファクトリーという概念の無かった時代に取り入れられてきた生産管理方式です。
しかし、現在トヨタ自動車はかんばん方式にデジタル技術を取り入れつつさらにパワーアップしており、さまざまな業界のプロジェクト管理の参考にされています。
見える化事例2:富士通の「COLMINA」
富士通では、工場内のさまざまなデータをつなげ、効率的に作業を行う「見える化施策」を推進しています。
富士通は、さまざまなニーズに応えるべく多品種少量生産を中心に行っています。
多品種少量生産は「ムダ」が発生しやすいことから運用が難しく、大量生産に比べより効率的に動かなければなりません。
そのため工場内の設備から記録されたデータをもとに生産状況・作業の進捗を可視化することで、作業の「ムダ」を発見し効率化を図っています。
富士通では収集したデータを過去のデータと照らし合わせ、少しでも異常があれば問題解決に努めるため、リスク回避に大いに役立ちます。
データは記録としての役割はもちろん、収集されたデータを分析し、プロジェクト管理だけでなく経営と生産現場をつなぐ役割を果たします。
日々変化していくデータを経営側が確認することで、迅速な経営判断が可能です。
富士通では自社の経験をもとに企業向けの見える化サービス「COLMINA」を展開し、見える化のノウハウを他社に共有し製造業の見える化推進に役立っています。
タスク・プロジェクト管理を
シンプルにわかりやすく
Jootoはカンバン方式のタスク・プロジェクト管理ツールです。
直感的に使えるレイアウト、親しみやすいシンプルなデザインが特徴です。
まずは無料で体験してみる
製造業の見える化の課題について

製造業のプロジェクト管理にはさまざまな課題があります。
見える化に取り組む際にはどのような課題が生じるか事前に知っておくことが大切です。
製造業の見える化の課題は以下の通りです。
- 工程計画がブラックボックス化している
- 「見える化」ではなく「見せる化」になっている
- データの取得方法が古い
- 部署に応じて適切な評価指標が設定できていない
ここでは4つの課題について詳しく解説します。
工程計画がブラックボックス化している
職人による作業は、定量化できない勘と経験によるものが多くあります。
定量化できない工程計画の問題は、スケジュール管理やプロジェクト管理が難しく、「ムダ」が発生しやすいデメリットがあります。
そのような工程計画は、特定の従業員しか把握していない「ブラックボックス化」になってしまうケースも少なくありません。
ブラックボックス化とは「いつ・なにを・どこで・どのくらいの時間」作業しているか分からない状況を表す言葉です。
担当者がオリジナルの「5W1H」を決めているため、経営者・管理者は正確な状況把握と予測を立てることができない状況にあります。
それに加えて突発的な作業の対応変更も難しく、従業員の中で作業の割り振りがうまくいかず最適な要員計画ができない恐れがあります。
ブラックボックス化の脱却の鍵を握るのは見える化であり、見える化の導入で誰が見ても分かるような作業工程を公開することで社内で情報を共有しましょう。
「見える化」ではなく「見せる化」になっている
製造業の見える化の課題の1つに、「見える化」が「見せる化」になっている問題が挙げられます。
見える化は本来さまざまなデータを元に分析し的確な判断を行い、効率的な作業ができるように改善を繰り返す施策です。
しかし、見える化がただデータを出力し共有しただけで満足する「見せる化」になってしまっている企業も多くあります。
データを収集しているだけでは問題解決につながらないため、課題解決に向けてアクションを起こすことが大切です。
見える化推進の本来の目的を今一度確認し、解決すべき課題を見誤ることがないようにしよう。
データの取得方法が古い
見える化を推進するにあたり、設備や機械が古いままでは正確なデータがとれない恐れがあります。
見える化にはデジタル化が必須になるので、監視カメラやIoTセンサーを取り付ける必要があります。
しかし、古い設備からのデータ移行にはコストがかかるため、なかなか手を出せないという企業も少なくありません。
国や自治体では、見える化を推進する企業をサポートする補助金制度があります。
コストを抑えて見える化施策を進めたいという企業は、役所に相談するとよいでしょう。
部門に応じて適切な評価指標が設定できていない
製造業の見える化の課題の1つに、部門に応じて適切な評価指標(kpi)が設定できていない点が挙げられます。
同じ評価指標である場合にも、部門によって計算方法や根拠となる数値が異なるケースは多くあります。
数値を見える化する際には、従業員の認識を統一させ誰もが分かりやすい判断基準の設定をしましょう。
タスク・プロジェクト管理を
シンプルにわかりやすく
Jootoはカンバン方式のタスク・プロジェクト管理ツールです。
直感的に使えるレイアウト、親しみやすいシンプルなデザインが特徴です。
まずは無料で体験してみる
製造業の見える化を推進する上で重要なポイント3選

製造業の見える化を推進する上で重要なポイントは以下の通りです。
- 製造工場の5Sに努める
- 社内共通の判断基準やルールを設定する
- 導入後も検証を繰り返し現場で使いやすい仕組みに変えていく
ここでは、3つのポイントについて詳しく紹介します。
製造工場の5Sに努める
見える化を導入する場合、5S(整理・整頓・清掃・清潔・しつけ)を行い環境を整えましょう。
不要なものがある場合は速やかに処分し、清潔な状態を保つことで気分を一心するのはもちろん余計な情報に左右されるリスクを防げます。
社内共通の判断基準やルールを設定する
社内共通の判断基準・ルールを作ることで従業員と同じ認識になるようにしましょう。
判断基準やルールは誰が見ても分かりやすいように設定し、社内で標準化してから見える化を導入することをおすすめします。
また、見える化の目的に関しても同様に全従業員の理解が得られるように丁寧に説明し、会社一丸となって取り組めるような体制づくりが大切です。
導入後も検証を繰り返し現場で使いやすい仕組みに変えていく
見える化は導入して終わりではありません。
導入後に起こった問題を解消し、効率化を図りましょう。
また、見える化のシステムが現場にとって使いやすいものになっているかを確認することも大切です。
よりよい成果を残すためにも検証を繰り返し自社にあった仕組みに変えていきましょう。
万が一トラブルが発生した場合にも、トラブルの原因を突きとめきちんと対処することが大切です。
トラブルが起こった際にはその都度対応マニュアルを更新し、再発防止に努めましょう。
タスク・プロジェクト管理を
シンプルにわかりやすく
Jootoはカンバン方式のタスク・プロジェクト管理ツールです。
直感的に使えるレイアウト、親しみやすいシンプルなデザインが特徴です。
まずは無料で体験してみる
Jootoは製造業の見える化推進の強い味方となる

Jootoは製造業の見える化推進に強い味方となるタスク・プロジェクト管理ツールです。
Jootoではかんばん方式を採用しており、使いやすさと分かりやすさの両方を兼ね備えている特徴があります。
基本操作はドラッグ&ドロップを中心とした誰でも簡単に利用できる仕様です。
初めてタスク・プロジェクト管理ツールを使用するという方も、抵抗なく利用できるでしょう。
また、ガントチャートを採用しており全体像が見やすくタスク漏れのリスクが解消できます。
従業員数が多く、多くのタスクのある製造業でもタスクの管理がしやすく、見える化を推進する場合にも最適なツールであると言えるでしょう。
Jootoの大企業向け新サービス「タスクDXプラン」
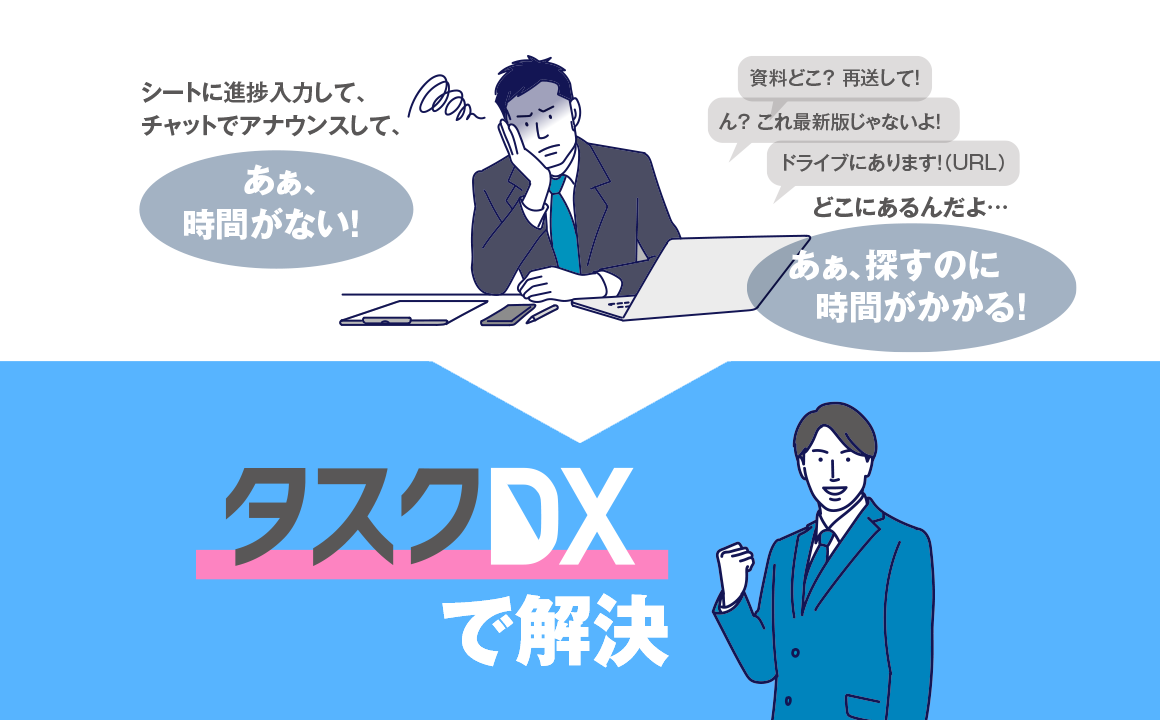
日々業務をこなしていく中で、以下のような悩みを抱えている方は多くいます。
- コミュニケーションツールの増加でやりとりをすぐに見返すことができない
- データファイルの保管場所が統一されておらず探すのに手間がかかる
情報の分散化により、本来必要のない作業が増えているという方も多いのではないでしょうか。
タスク・プロジェクトをより効率的に行いたい際には、2023年2月よりサービスを開始した「タスクDXプラン」をおすすめします。
JootoのタスクDXプランを利用することでJootoに情報を一本化させ、探す手間やコミュニケーションの手間を省けます。
タスクDXプランは人数に応じて利用金額が変動せず定額無制限でライセンスが取得できるため、従業員の多い企業でも安心して使えるサービスとなっています。
製造業の「見える化」を成功させたい場合には、ぜひJootoをご検討ください。
Comments are closed.