「物と情報の流れ図」をご存じですか?
生産性の向上や効率化が声高に叫ばれる昨今、トヨタ自動車が生み出した「物と情報の流れ図(VSM)」を活用することで、適切な現状分析や現状把握に役立ち、リードタイム短縮へつなげることができます。
物と情報の流れ図を作成するプロセスやメリット、注意点などを紹介しますので実践してみてください。
タスク・プロジェクト管理を
シンプルにわかりやすく
Jootoはカンバン方式のタスク・プロジェクト管理ツールです。
直感的に使えるレイアウト、親しみやすいシンプルなデザインが特徴です。
まずは無料で体験してみる
目次
トヨタ式「物と情報の流れ図(VSM)」とは
VSMはValue Stream Mapping(バリューストリームマッピング)を略した言葉で、「モノ」と「情報」をひとつの流れ図にしたフローチャートの一種です。
「物情(ものじょう)」と呼ばれることもあります。
トヨタ自動車がトヨタ生産方式(TPS)のなかで確立した手法です。
主に製造業で使われるフロー図で、物がどこからきてどこへ行くのか、その流れを情報の流れとひとつの図にまとめることで、全体の流れを見える化でき、どこで停滞が起きているのか把握することができます。
物と情報の流れ図(VSM)によって無駄が改善され、仕事の標準化や全体のリードタイム短縮に役立てることができます。
物と情報の流れ図(VSM)の目的・用途
製造業では、業務に携わる人数も多く、関わりのある工程以外の動きがわかりづらいことがよくあります。
物と情報の流れ図(VSM)で前の工程から後の工程までの流れをとらえることで、製品がどこからきてどのように流れていくのかや、どのような情報をもとに作業がおこなわれているのかを見える化し、共通認識を持てるようにすることが、物と情報の流れ図(VSM)の目的のひとつです。
また現状把握・現状分析の用途としても使われます。
問題点や課題が発生した場合、すみやかに対応しなければいけませんが、どの部分に課題があるのか把握し、分析する必要があります。
物情(VSM)によって、物流の停滞が起こりやすい工程(ボトルネック)を把握することで、企業がおこなう現場改善、品質改善のための小集団活動などに役立てることができます。
トヨタ生産方式(TPS)とは
物と情報の流れ図(VSM)は、トヨタ生産方式(TPS:Toyota Production System)のなかのひとつの手法です。
トヨタ生産方式(TPS)は、クライアントの要望を満たしつつ、利益の最大化を追及する生産方式です。
無駄を徹底的に排除するためにトヨタ自動車で確立されました。
ジャストインタイム生産方式・リーン生産方式とも呼ばれています。
顧客にとって価値のある作業や業務(付加価値)以外の7つの無駄(作りすぎ、手待ち、運搬、加工、在庫、動作、不良を作る)を定義し、排除していきます。
一般的な生産方式では、需要を予測し生産計画を立て、実行されます。
各工程に在庫を置くことで、ラインを止めることなく、トラブルや需要の変化などにも、その都度、対応できるようにしていますが、どうしても作りすぎなどの無駄が生じてしまいます。
一方、トヨタ生産方式(TPS)では、「必要なもの」を「必要な量」、「必要なとき」に供給するという考え方です。
また「異常が発生したら機械をただちに停止し、不良品を造らない」という考え方(トヨタ自動車では「自働化」と呼ばれています)もトヨタ生産方式の柱のひとつです。
在庫は最小限になり、必要な時に材料が発注され、すみやかに製造ラインに流されます。
在庫の管理や発注数量の予測などは必要なく、リードタイムが短縮できるため、人件費の削減にもつながります。
ただし平準化できない生産には向いていません。
また、在庫を持たないため、大量購入によるコストダウンが望めないというデメリットもあります。
製造業における物と情報の流れとは
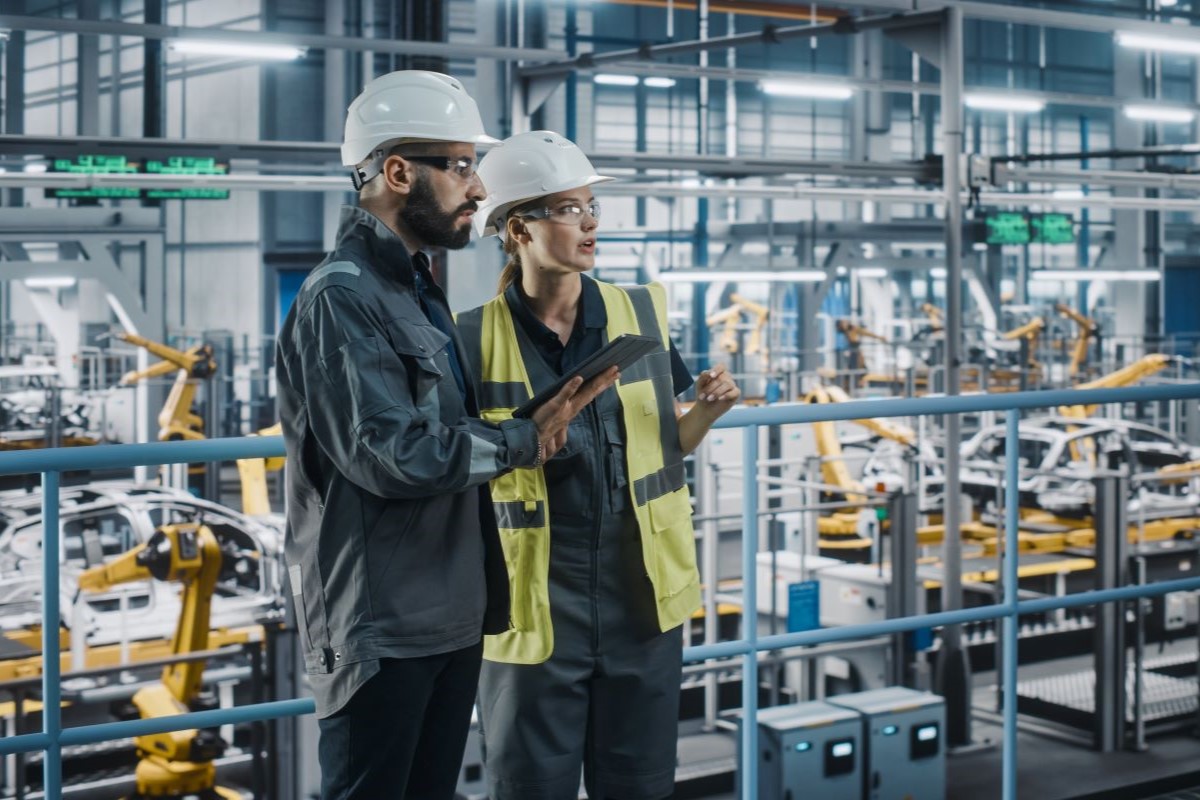
製造業では、常に物(製品)と情報が流れています。
どのような流れで製品が制作され顧客へ納められているのでしょうか。
基本となる流れについて解説します。
情報の流れ
製造業では、顧客から注文を受注し、注文情報に応じて製造がはじまります。
顧客の要件などから、生産量にあわせてサプライヤーへ何をどれだけ発注するのか決定し、部品などの材料を発注します。
製造ラインでは、品質管理がおこなわれ、その情報は要件などとともに共有されます。
その手段としてかんばん方式が用いられることもあります。
そして最後の検査工程後、製品の品質情報などを顧客に伝え納品します。
製品(モノ)の流れ
製造に必要な材料が自社にない場合、サプライヤーから仕入れた材料(部品など)が納品されます。
製造工程では、前工程から後工程へ製品が流れていき、ポイントごとに、品質などのチェックがおこなわれ、完成品が顧客へ納品されます。
かんばん方式などを活用すると、モノと情報を一元的に管理することができ、業務の流れが明確になります。
人の流れ
物の流れとともに、作業する人の流れも発生します。
人によって品質が変わってしまうということを防ぐために標準作業を定め、品質に偏りが出ないようにします。
タスク・プロジェクト管理を
シンプルにわかりやすく
Jootoはカンバン方式のタスク・プロジェクト管理ツールです。
直感的に使えるレイアウト、親しみやすいシンプルなデザインが特徴です。
まずは無料で体験してみる
物と情報の流れ図(VSM)のメリット
物と情報の流れ図(VSM)のメリットについて解説します。
下図のように顧客より製品の発注を受けてから、製品が完成し納品されるまでの流れが示されていることが多いです。
特に大規模な工場の場合、各工程の担当者は、自分の工程の流れは把握していても、全体的な流れはわからないということが多々あります。
それでは部分最適しかおこなえず、上流の工程でトラブルが起きても対応できないということになってしまう可能性があります。
物と情報の流れ図(VSM)では、工程ごとの細かいフローチャートではなく、全体の流れを大きく把握し、全体最適に役立ちます。
また、物と情報の流れ図(VSM)によって、全体の流れを把握することで、リードタイム短縮の阻害要因を見つけることが出来る点が大きなメリットのひとつです。
リードタイムとは、工程や作業の始めから終わりまでにかかる所要時間(期間)のことです。
全体像を把握できることで、リードタイム短縮のボトルネックとなっている工程がわかるようになり、どこから問題の解決・改善を進めれば良いのか手順がわかるようになります。
また、VSMがあることで、関係者全員に共通認識ができます。
チーム全体のコンセンサスを得やすくなり、業務改善が進めやすくなります。
品質向上を目指すQC活動においても、物と情報の流れ図(VSM)で問題となっている工程を見つけられる可能性があります。
QC7つ道具(パレート図・特性要因図・グラフ・ヒストグラム・散布図・管理図・チェックシート)などを用いて適切な品質管理や課題の解決を目指しましょう。
VSM(バリュー・ストリーム・マップ)作成のプロセス
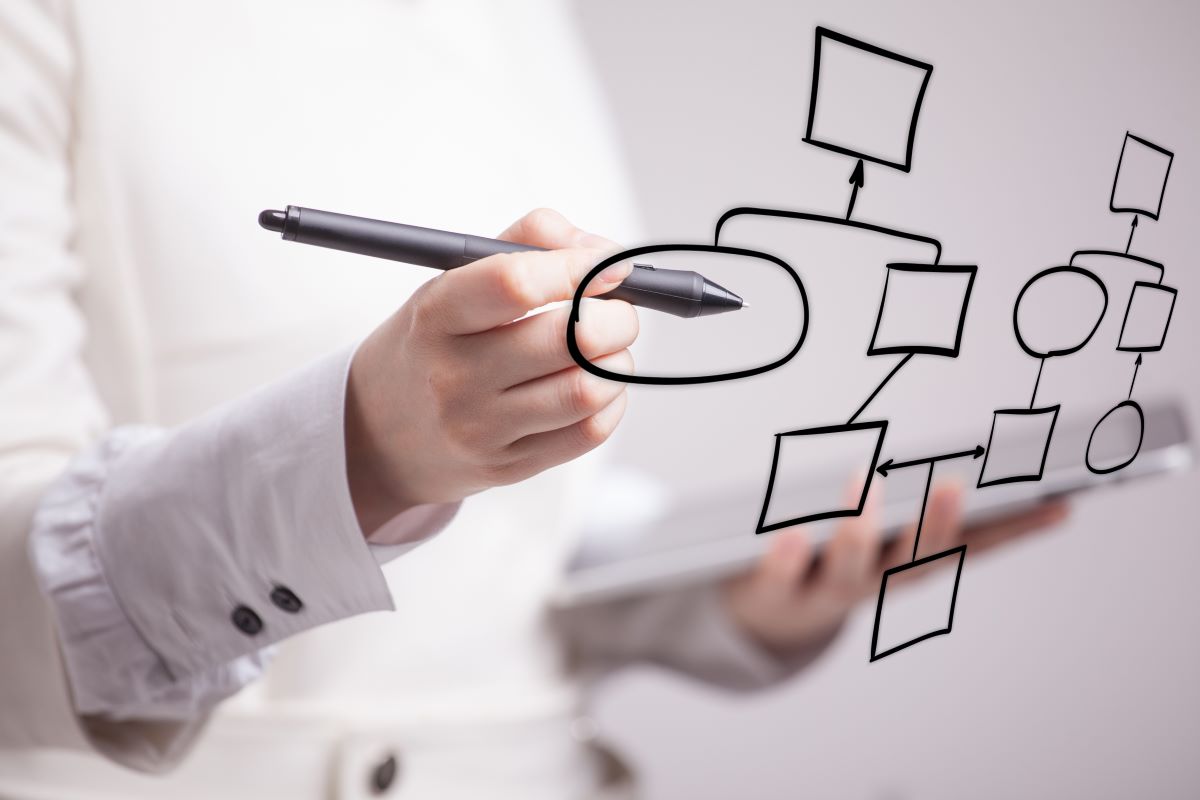
リードタイムの短縮や現状把握・現状分析のために、物と情報の流れ図(VSM)が役立つことがわかりました。
では、どのように物と情報の流れ図を作成すれば良いのか、具体的なプロセスや書き方を紹介しますので実践してみてください。
1. 物と情報の流れ図(VSM)のスコープ(範囲)の決定
まずはどこまでをフロー図に落とし込むのか、そのスコープ(範囲)を決定します。
流れ図にする製品の決定や、どこまでの範囲を図に入れるのかを明確にします。
多くの製品を製造している会社の場合、すべての製品のVSMを作成したくなるかもしれませんが、製品によって工程や材料(部品)が異なるため、まずは製品を絞り込みましょう。
ひとつの製品につき、ひとつの図を作成するのが望ましいです。
また、サプライヤーまで図に入れるのか、すべての工程を入れるのか、などを決定します。
複数の企業が関わっている場合、そのすべての流れを記載する方法もありますが、複雑化してしまうため、自社内の流れにだけ限定する方法もあります。
2. 業務とモノの流れについて記載する
まずは、業務内容と、物の流れを記載した図を作ります。
出発点(工場など)となる場所から終着点(顧客など)まで描き、流れに沿って矢印を書きます。
情報を整理・整頓し、正確な図が書けるようにしておきましょう。
記号などを用いてなるべく見やすくわかりやすい図にします。
業務の物の流れがまとまったら、いつ、だれが、などの詳細情報を必要に応じて書き足しましょう。
物の流れとともに人の流れが発生するため、図に登場する人物についてもスコープを決めておき、書き足す必要も出てくるかもしれません。
だれが作業しても、同じ結果になるよう、標準作業や作業手順を定めておくことも大切です。
3. 情報の流れを記載する
次に情報の流れを記載します。
物の流れと区別がつくように、色分けなどをしておきましょう。
注文情報や仕入れの発注、検査結果や納品書、請求書などの情報を書いていきます。
情報の種類によっては、物と情報が同時に動いている場合もあるため、それについては省略することもあります。
4. 停滞が起こる箇所(ボトルネック)
流れ図のなかで、停滞が起こる箇所(ボトルネック)がわかっている場合はそこに印をつけます。
たとえば、図を作成していくなかで曖昧だった箇所はありませんか?そこがボトルネックになっている可能性があります。
担当者などに確認をおこない、課題を発見しましょう。
5. 問題点・課題をリスト化する
物と情報の流れ図によって、現状把握・現状分析ができ、個々の工程の業務フロー図だけでは見えてこなかった問題点や課題、無駄が見えてきます。
ボトルネックとなっている箇所や見えてきた課題についてリスト化し、明確化します。
そして、PDCAサイクルを回すなどして、業務改善に役立てましょう。
物と情報の流れ図(VSM)作成の注意点
物と情報の流れ図(VSM)は全体像を把握するために作成しますが、以下のような注意点があります。
1枚の紙にまとめる
スタートからゴールまでの物と情報の流れを見るためのものなので、詳細な業務フロー図とは異なります。
必要のない細かい情報は書く必要がありません。
あまり細かい情報が増えてしまうとプロセスの全体像がわからなくなってしまいます。
全体を俯瞰して見られるよう、1枚にまとめて書きましょう。
記号などを使ってわかりやすく
多くの人が見ることになる図なので、わかりやすくすることが大切です。
また、字が多いと見にくくなってしまうため、記号などを活用してシンプルで見やすい図にすると良いでしょう。
何が必要で、何がいらないのか見極めることが大切です。
繰り返して精度を高める
いきなりスコープを広くし、末端のサプライヤーまで図に入れようとしても上手くいきません。
まずは、目の届く自社の構内物流の範囲の図を作り、現場改善をおこなうごとに範囲を広げ、精度を高めていくと良いでしょう。
物と情報の流れ図(VSM)は現状を把握し、さまざまな阻害要因を発見、改善するのには役立ちますが、製造業では、製品の進捗管理なども必要になります。
作成した物と情報の流れ図(VSM)を活かすためにも、進捗管理に役立つツールの活用がおすすめです。
タスク・プロジェクト管理を
シンプルにわかりやすく
Jootoはカンバン方式のタスク・プロジェクト管理ツールです。
直感的に使えるレイアウト、親しみやすいシンプルなデザインが特徴です。
まずは無料で体験してみる
製造工程の全体を管理するには「Jooto」がおすすめ

物と情報の流れ図(VSM)は、現状把握・現状分析に役立て、リードタイムの短縮につながることがわかりましたが、実際に製造ラインが動きだしたときに、リアルタイムで進捗管理・生産管理・品質管理をするには、タスク・プロジェクト管理ツール「Jooto」の活用が便利です。
Jootoはシンプルで使いやすい、かんばん方式のタスク・プロジェクト管理ツールです。
操作方法が簡単なため、誰でもすぐに使えるようになり、教育コストがかかりません。
製造業でかんばん方式はよく使われている手法ですが、Jootoではデジタルでおこないます。
工程ごとに管理できるほか、タスクごとにロットナンバーを割り振れば、ロットごとの管理も可能になります。
また、製品の進捗を可視化するにはガントチャートが便利です。
Jootoなら、タスクカードを入力するだけで自動的にガントチャートが作成されます。
各工程の担当者が、現在の進捗状況をそれぞれ入力することでデータが一元化されるため、管理者にとっても確認の手間がなく、リアルタイムの進捗状況を確認できます。
製造業には「タスクDXプラン」がおすすめ
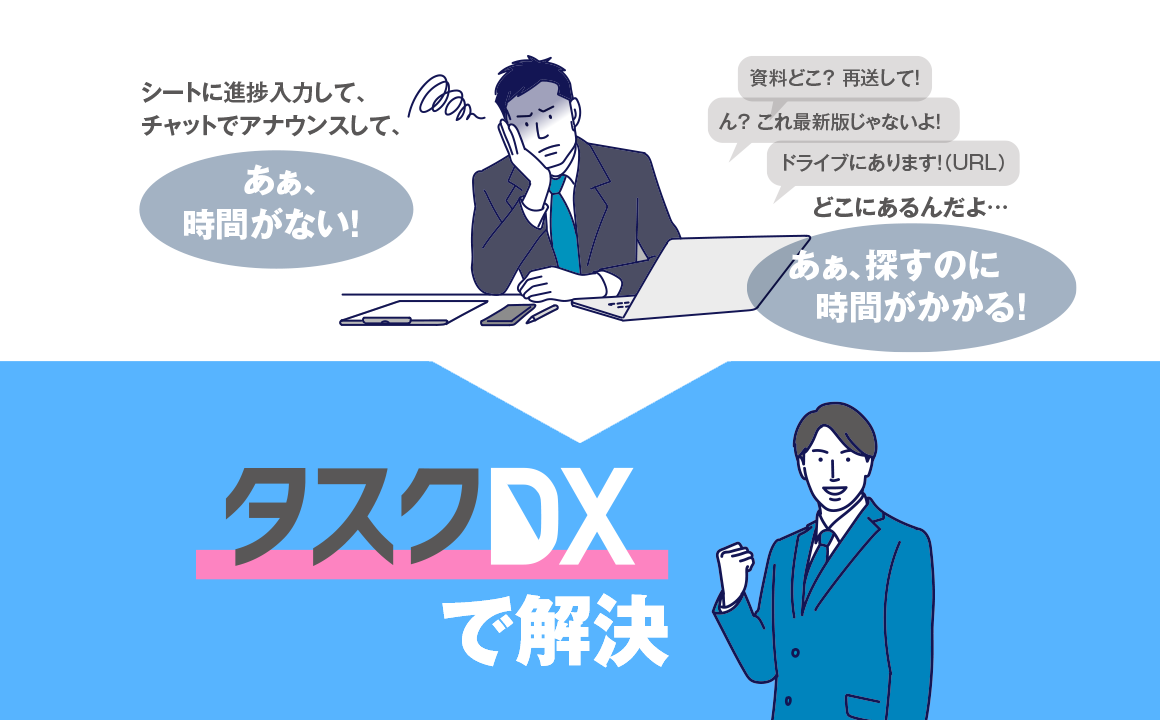
大きな工場などでは工程の数や従業員の数が多く、全ての情報を共有するのは難しくなります。
タスクDXプランでは膨大なストレージによって、全ての情報を一元管理することが出来るようになり、多くの人員を抱えている大規模製造業でも対応することが可能です。
また、セキュリティも万全で、従来からの法人向けプランであるビジネスプランの強固なセキュリティが適用されます。
機密情報を扱うことの多い工場でも安心して使用していただけます。
製造業での、進捗管理・生産管理・品質管理に、ぜひJootoをご検討ください。
Comments are closed.