かつては同じ製品を量産する少品種大量生産が製造業の主流でしたが、近年では多様化する顧客ニーズに対応するために、多品種少量生産へと変化しつつあります。
多品種少量生産は製品ごとに作業工程が異なるため、作業が複雑になりやすく、少品種大量生産方式と比較するとコストが高くなります。
そのため、企業はこれまでの製造方式を根本から見直し、より効率的な製品づくりを実現していく必要があります。
効率的な製品づくりのキーワードとなるのが「平準」です。
当記事では、製造業における平準化の必要性や平準化の具体的な手順、平準化推進のポイントなどを解説します。
トヨタが開発したトヨタ生産方式の解説や管理ツールの紹介もするので、ぜひ参考にしてみてください。
タスク・プロジェクト管理を
シンプルにわかりやすく
Jootoはカンバン方式のタスク・プロジェクト管理ツールです。
直感的に使えるレイアウト、親しみやすいシンプルなデザインが特徴です。
まずは無料で体験してみる
目次
生産管理の平準化とは
平準とは、「でこぼこしたものを平らにならす」ことです。
製造業における生産管理の平準化とは、生産量と生産する品目を均等にすることや、リードタイム・コストをそろえることを意味します。
リードタイムとは、受注から納品までに要する時間のことです。
リードタイムを短縮することで、納期の前倒しが可能になり、顧客のもとにいち早く製品を届けられるようになります。
つまり、「生産が平準化された状態」とは、生産量や品目のばらつきをならし、常に一定の生産量や生産品目が維持され、納品までにかかる時間も均等化された状態のことです。
生産管理を平準化することで余分な仕掛や完成品のムダを取り除くことができ、過剰な生産能力の維持や過剰な人員配置が不要になります。
平準化生産と対比されるのが、ロット生産です。
ロット生産とは、ロット単位で同じ製品を生産し、生産が終わり次第別の製品をつくる方式です。
製品ごとに専用ラインを装備するほど生産量が多くない場合や、生産ラインに流す製品に合わせて装置を変更すれば複数の種類の製品を製造できる場合などに採用されます。
ラインの効率が良い点がロット生産のメリットですが、最大生産量に合わせて人員や設備を投入するため、ムダが多いところがデメリットです。
具体的には、今日100個生産した製品を、次の日には1,000個要求される場合もあるため、生産計画のばらつきが大きく、過剰在庫を抱えることになったり、在庫切れが生じたりします。
結果的に原価の高い製品になってしまいます。
標準化との違い
製造業において平準化とともに重要な意味をもつ言葉に標準化があります。
標準化とは、業務の手法を統一して誰でも実行できる状態にすることで品質を一定に保つことです。
たとえば、作業の手順を詳細にマニュアルに記載することで、誰が担当しても一定のクオリティで製品をつくれるようになります。
あるいは、ISOやJISなどの社外規格を用いることで、製品の品質を均一化できます。
一方の平準化は、生産量や品目を均等にすることに焦点を当てた考え方です。
受注数量に応じて生産量を変えるのではなく、月単位や日単位で生産量を一定化させます。また、生産する品目の数も一定に保ちます。
タクトタイムとサイクル・タイムの関係性
平準化を考える際にリードタイムとともに押さえておきたい言葉にタクトタイムとサイクル・タイムがあります。
タクトタイムとは、1つの製品を完成させるまでにかけられる時間のことです。
サイクル・タイムとは、1つの製品が完成するまでに実際にかかる時間を示します。
タクトタイム=サイクル・タイムであれば、必要な生産能力と実際の生産能力が等しい状態を保っていることになります。
タクトタイムとサイクル・タイムは、どちらも「1つの製品の生産にかかる時間」を示しますが、視点が異なります。
サイクル・タイムは、生産者側の設備能力を考慮した生産者視点の時間ですが、タクトタイムは、生産者側の都合を考慮しない顧客視点の時間です。
平準化生産の基本は、需要に応じて毎日同じペースで生産を進めることです。
タクトタイムはその基準の役割を果たし、「必要なものを、必要なときに、必要なだけ」製造するための指標を提供します。
そのため、平準化の推進にあたっては、タクトタイムを意識して各工程の人員配置などを検討することが大切です。
タスク・プロジェクト管理を
シンプルにわかりやすく
Jootoはカンバン方式のタスク・プロジェクト管理ツールです。
直感的に使えるレイアウト、親しみやすいシンプルなデザインが特徴です。
まずは無料で体験してみる
製造業で平準化が求められる理由
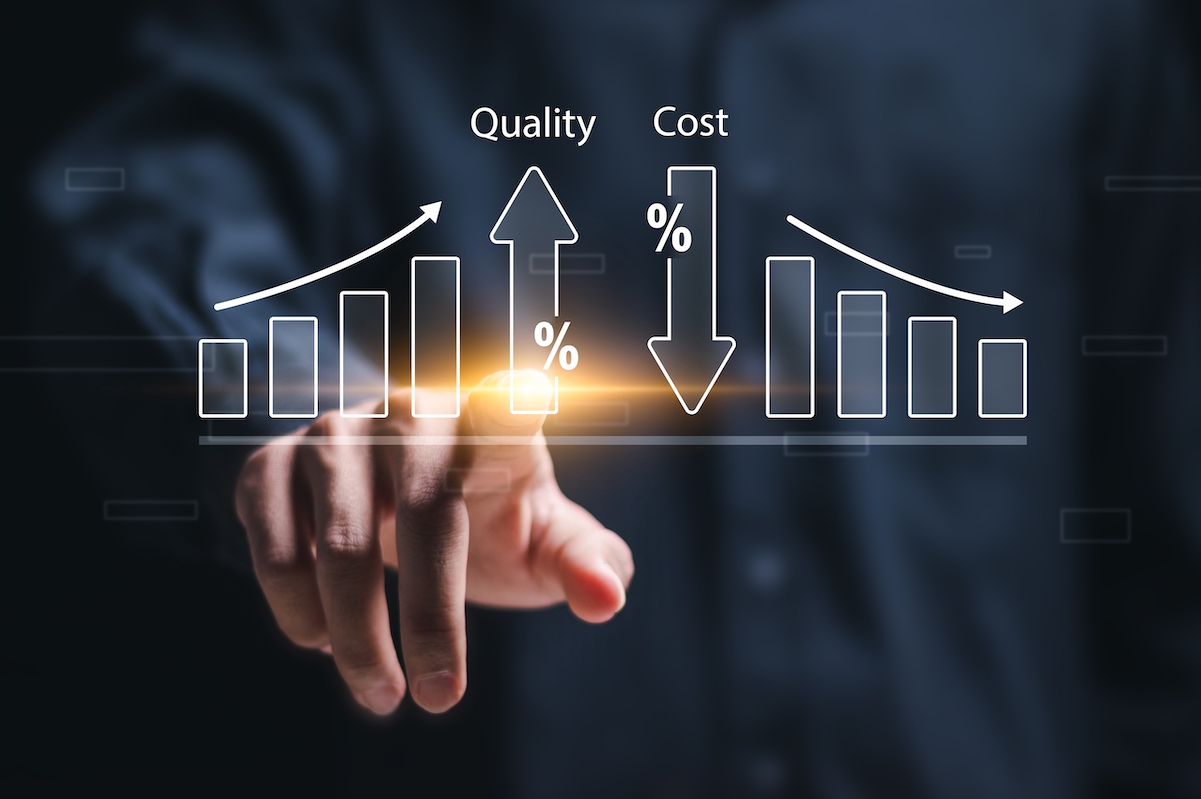
平準化は、業務効率化や生産性向上を目的として、製造業だけでなくあらゆる業種で重視される考え方ですが、とくに製造業において導入効果が大きいとされています。
製造業で平準化が求められる理由について以下の4つの観点から詳しく解説します。
- コストの削減につながる
- 品質向上につながる
- 在庫量の適正化につながる
- 従業員の負荷が軽減される
コストの削減につながる
生産管理の平準化は、人件費削減に効果的です。
平準化を導入していない場合、受注数量に応じて生産量が変化するため、7月は100個、8月は500個という様に、時期によって生産量が変わることが特徴です。
繁忙期の受注量に備えて人員を確保しなければならないため、受注数量が少ない時期にはムダな人件費が発生します。
生産量が平準化されれば、余剰人員を確保する必要がなくなるため、人員計画を立てることが容易になり、人件費のコストカットにつながるのです。
品質向上につながる
平準化によって生産計画が立てやすくなり、結果的に製品の品質向上につながります。
生産の平準化がなされていないと、受注数量が集中する繁忙期の生産計画にムリが生じます。現場従業員の長時間労働によって仕事量の増加分をカバーすることになり、過労による品質低下やヒューマンエラーの発生は避けられません。
また、設備を長時間稼働させなければならず、故障の頻度が高くなります。
故障の結果、不良品率が高くなるリスクは軽視できません。
製品の品質向上のためには、平準化によって余裕をもった生産計画を立てることが不可欠です。
在庫量の適正化につながる
平準化はあらかじめ需要を予測し、計画に沿って製品を製造する手法のため、完成品在庫が過不足するリスクを軽減できます。
平準化がなされていないと、需要が急激に増えた際に納期遅れが発生し、顧客の信頼を失うことにもなりかねません。
反対に、予想に反して需要が減った場合は過剰在庫を抱えることとなり、製品の品質が下がる、保管のためのムダなコストが発生するといった問題が発生します。
生産の平準化によって常に適正な完成品在庫を保てるようになることは、大きなメリットです。
従業員の負荷が軽減される
工程や時期によって業務量のばらつきが大きく、生産能力を超える生産をしなければならない状況は従業員の残業時間の増加を招き、ミスの要因となります。
平準化に取り組むことによって業務量のムラが解消されて先の見通しがつきやすくなり、余裕をもったスケジューリングが可能になります。
従業員の負荷が軽減され、働きやすい環境が整うことで、生産性向上へとつながっていくでしょう。
また、人的リソースの適正配置へつながることも、大きなメリットといえます。
タスク・プロジェクト管理を
シンプルにわかりやすく
Jootoはカンバン方式のタスク・プロジェクト管理ツールです。
直感的に使えるレイアウト、親しみやすいシンプルなデザインが特徴です。
まずは無料で体験してみる
トヨタ生産方式「ジャストインタイム」とは
平準化を取り入れた製造業の効果的な生産方式としては、トヨタの「ジャストインタイム」が知られています。
トヨタ生産方式とは、以下の2つを柱とした方式です。
- 自働化:人の働きを機械に置き換え、生産性をアップさせる
- ジャストインタイム:無駄を排除し生産効率を向上させる
トヨタ生産方式の2つの柱のうち、ジャストインタイムは平準化生産が実現できていることが前提となる考え方です。
ジャストインタイムとは、「必要なものを、必要なときに、必要なだけ」つくる生産方式のことで、主に過剰在庫をもたないことを目的としています。
具体的には、トヨタでは、注文が入るとまずは生産ラインの先頭に生産指示が出されます。
組立ラインはすべての種類の部品を少量ずつ備えておき、利用した部品の分だけ前工程である部品を製造する工程へ引き取りにいきます。
このような後工程引き取り式の生産方法が、ジャストインタイム方式です。
「平準化ができていない状態=生産量に偏りがある状態」でジャストインタイムを導入すると、後工程が引き取った分だけ前工程が部品を生産することが難しく、部品の欠品が生じたり、部品の過剰在庫を抱えたりすることになってしまいます。
生産管理を平準化する手順
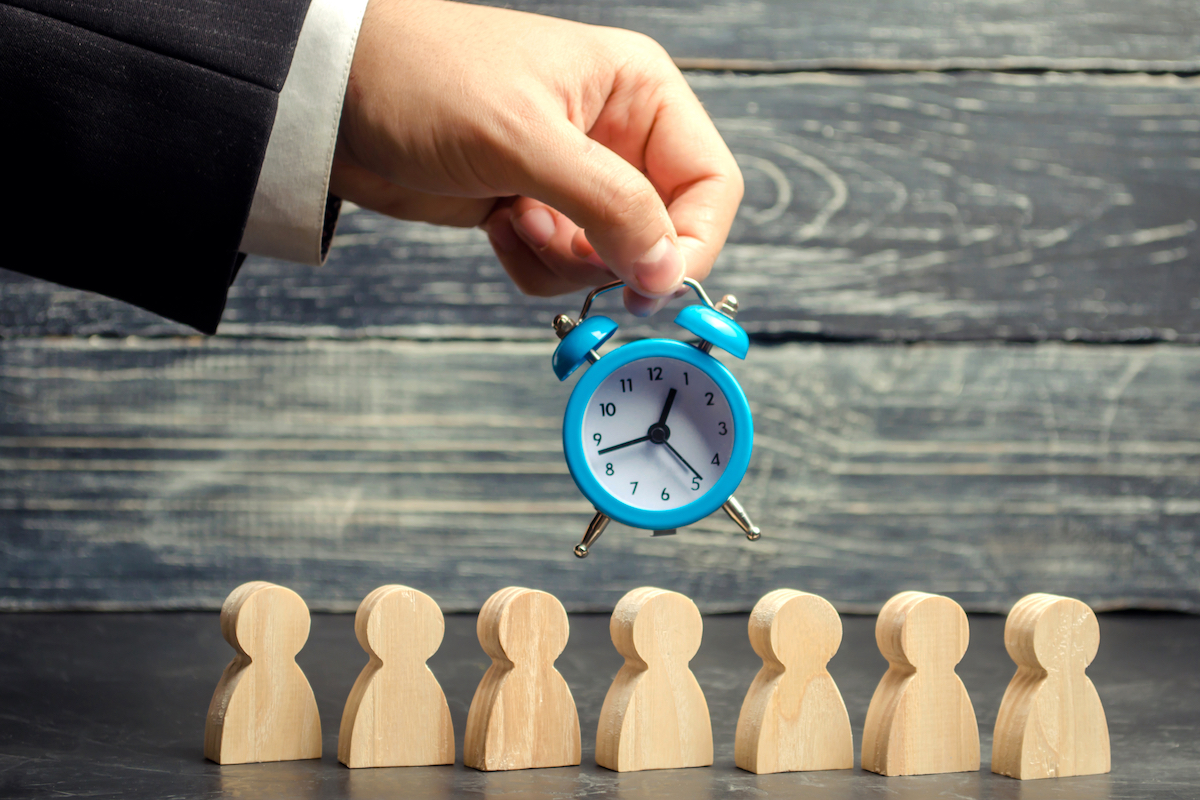
生産管理の平準化は一気にすすめることは難しく、段階的に取り組んでいくことが大切です。
平準化の手順は、以下のとおりです。
- 平準化したい工程全体を見える化する
- 見える化した工程を3つの時間に分類する
- ムダ時間をカットする
- 内段取り時間を短縮する
- 外段取りを工夫する
それぞれの詳しい内容を解説します。
1. 平準化したい工程全体を見える化する
まずは平準化したい工程全体を分析し、見える化します。
多品種生産ラインの場合、生産する品種を切り替える際に時間がかかる傾向があります。
生産現場の技術者が具体的に何をしているのか、品種切り替えにかかる時間がどのくらいかを詳細に洗い出していきます。
表などにまとめて見える化することがポイントです。
「次の部品の製造に取り掛かるために必要な装置を探す時間」など、細かな時間のロスも見逃さずに明らかにしていきましょう。
2. 見える化した工程を3つの時間に分類する
前段階で見える化した工程を、以下の3つの時間に分類していきます。
- 内段取り時間
- 外段取り時間
- ムダ時間
内段取りとは、機械の部品交換など、機械や作業を一旦ストップしてから作業しなければならない段取り作業のことです。
外段取りとは、機械を稼働させながらおこなえる作業のことを指します。
必要な工具や部品が見つからずに探している時間など、本来必要ない時間はムダ時間に該当します。
3. ムダ時間をカットする
分類した3つの時間のうち、ムダ時間をカットします。
内段取りや外段取りの時間は、製品を製造するうえで必ず発生する時間ですが、工具や部品、マニュアルを探している時間などは徹底的にカットすべき時間です。
部品置き場を整理整頓してラベリングしたり、作業手順を記したマニュアルや資料を目につく場所に常設したりすることで、ムダ時間は減らしていけます。
一つひとつのムダ時間は小さくても、積み重なることで大きな時間のロスとなります。
これまで当たり前にかかっていた時間を根本的に見直すことで、業務効率が大きくアップするでしょう。
4. 内段取り時間を短縮する
内段取り時間は機械や作業をストップして作業にあたる時間のため、生産性に大きな影響を与えます。
まずは、本当に機械を停止させる必要があるのか確認してみましょう。
事前に部品を用意しておくことやシステムの導入などにより、機械を稼働させたまま作業できるようになる可能性があります。
これまでの常識に捉われず、さまざまな角度から検証してみることが大切です。
内段取りの時間が短縮できれば、作業フロー全体の時間が短縮され、生産性向上へとつながります。
5. 外段取りを工夫する
内段取りが効率化され時間短縮が実現すると、これまで外段取りとして機械を稼働させたまま作業していた業務が間に合わなくなる恐れがあります。
内段取りの効率化の効果を最大限に活かすためにも、外段取りの方法を工夫する必要があります。
たとえば、導線を工夫して今までよりも短時間で作業できるようにしたり、他の工程の作業員にサポートしてもらう体制を構築するなどの方法があります。
タスク・プロジェクト管理を
シンプルにわかりやすく
Jootoはカンバン方式のタスク・プロジェクト管理ツールです。
直感的に使えるレイアウト、親しみやすいシンプルなデザインが特徴です。
まずは無料で体験してみる
平準化推進のポイント
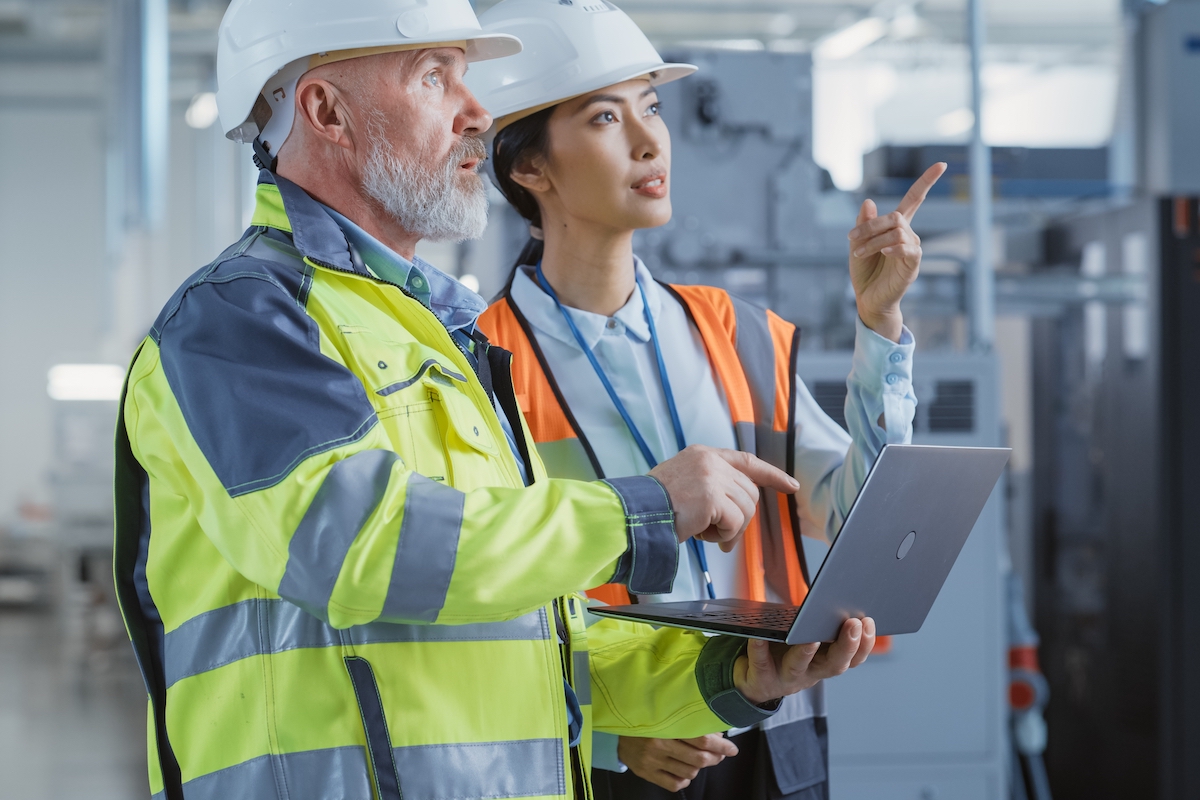
これまでの製造プロセスを大きく変える取り組みは、少なからず生産現場に混乱を招きます。
平準化を推進する際は、従業員の理解を得ながら全社的な取り組みとして実行していく必要があります。
平準化推進のポイントは、以下のとおりです。
- 平準化自体に固執しない
- 平準化する製品に優先順位を付けて取り組む
- 作業者の技量がそろうように努める
- 生産計画に柔軟性をもたせる
- マニュアル化を進める
- 管理システムを導入する
それぞれの詳しい内容を解説します。
平準化自体に固執しない
平準化は手段であって目的ではありません。
平準化に固執するあまり生産現場の実態にそぐわない施策を実行したり、コストが増えたりしては本末転倒です。
平準化の目的は、完成品在庫の適正化やリソースの最適化によってコスト削減や品質向上を実現することです。
企業の規模や扱う品種によって適切な生産計画は異なります。
平準化のゴールを見誤らず、自社にとってベストな施策を模索する姿勢が大切です。
平準化する製品に優先順位を付けて取り組む
多品種を製造する企業がすべての製品の製造工程を平準化するためには膨大なコストと時間がかかります。
一部の製品に的を絞るなど、優先順位を付けながら平準化を進めることがおススメです。
平準化を進める過程で課題が浮き彫りになることも多いため、それを次の製品の平準化に活かしていけます。
まずは過剰在庫が発生しやすい製品から平準化するなど、方針を決めてから取り組むとよいでしょう。
作業者の技量がそろうように努める
工場の作業者の技量に差がありすぎると、平準化の実現は難しいでしょう。
平準化を推進する前提として、作業者の技量がそろうように教育することが大切です。
工場のOJT体制の確立や業務のマニュアル化によって、誰が担当しても一定レベルの成果がでるよう工夫しましょう。
技量・力量をそろえる取り組みは、業務の属人化を防ぎ、ナレッジを継承していくうえでも効果を発揮します。
生産計画に柔軟性をもたせる
過去の実績をもとに生産計画を立てたとしても、未来の生産量を正確に予測することは不可能です。
仮に顧客から受注の内示を受けていたとしても、急なキャンセルが発生する場合もあります。
こうした変化に迅速に対応できるように、生産計画に柔軟性をもたせることが大切です。
生産計画はできるだけ短期サイクルで作成し、需要の変動に合わせて適宜見直しを図ることがポイントです。
マニュアル化を進める
作業者が同じレベルのパフォーマンスを発揮できるように、誰にとってもわかりやすいマニュアルを作成しておくことが大切です。
担当の作業者が急な事情で不在の際も、他の人が代替できるようにしておくと、作業が滞りなく進行します。
管理システムを導入する
生産管理の平準化を実現するためには、製造工程を見える化し、作業の「ムリ・ムダ・ムラ」を明確にするステップが不可欠です。
ExcelやWordなどを活用して作業を書き出していくことも可能ですが、他の作業者との共有や情報更新の利便性を考慮すると、管理システムの導入がおススメです。
管理システムの導入にあたっては、他社の導入事例を参考に、自社のニーズに合致したシステムを選ぶことが大切です。
工程ごとにタスクをかんばん方式で管理できるシステムを導入すれば、作業量の偏りを一目で把握できるため、効率的に平準化を進められるでしょう。
Jootoを使って製造工程を見える化しよう

Jootoはシンプルで使いやすいかんばん方式のタスク・プロジェクト管理ツールです。
基本的な操作はドラッグ&ドロップだけのため、誰でも問題なく使いこなせます。
製造業の生産プロセスを平準化するためには、工程ごとのタスクを細かく洗い出し、ムダを徹底的にカットしていくことが大切です。
Jootoを活用すれば、工程ごとのタスクを簡単に可視化でき、どこに偏りがあるのか一目で把握できます。
また、スマートフォンやタブレット、パソコンなどさまざまなデバイスからアクセスできるため、離れた工場同士の情報共有も容易です。
製造プロセスの平準化に取り組みたい場合は、ぜひタスク・プロジェクト管理ツールJootoの導入をご検討ください。
Comments are closed.